Digital tool solutions revolutionise processes
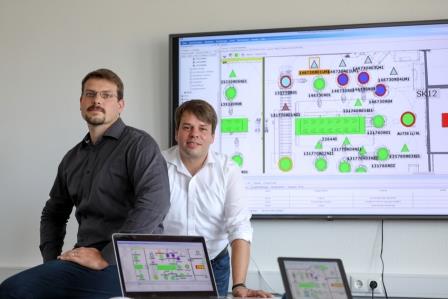
With its project management solution, “COMAN Software GmbH” revolutionises system and machine construction. Its software combines digital construction planning with detailed scheduling. The founder duo draws on long-standing experience in software development and incorporate it with fresh entrepreneurial spirit. From northern Saxony-Anhalt, the start-up is now attracting new industries and customers.
Machine and system builders are familiar with the issue. Planners design systems like production lines and create a digital layout. Practical implementation takes place on site. Various players use the digitised models - but in an analogue form as a print-out or written script. Changes, current requirements or the processing status are often noted in writing. Communication to all those involved is frequently complicated by the fact that these notes “disappear”. Mats-Milan Müller says the reason for this is “media discontinuity”. “This is where our work comes in”, the Marketing Head of “COMAN Software GmbH” says. The company from Stendal has set itself the objective of increasing the planning quality in large projects. “How can the status be recorded and illustrated in a transparent manner?” “How can all those involved - from the management level to the contractors’ employees - be kept up to date?” The start-up founded in 2018 provides an answer to these questions, thanks to its software and its associated possibility of managing the project not only via desktop computers but also via app with a smartphone or tablet.
Start-up starts with ideal prerequisites
Both Managing Directors, Timur Ripke and Sven Kägebein, have been dealing with the development of these solutions for many years. The call for this kind of software came in 2010 from the automotive industry. The “Innovationsgesellschaft für fortgeschrittene Produktionssysteme in der Fahrzeugindustrie mbH” (inpro) was the one that heard it. In the research community, which companies such as “Daimler”, “Siemens”, “Sabic”, “Thyssenkrupp” or “Volkswagen” are part of, the software was initially exclusively developed - for the organisation and planning of plant construction projects according to the “inpro” community requirements. It reached its market maturity in 2015. The spin-off “COMAN Software GmbH” was founded three years later. This was a significant and right step for both founders. “The time was just right and the starting point was ideal”, Timur Ripke says. “We had a tried and tested software and a renowned customer base which had already come to appreciate it.”
Stendal headquarters has logistic and economic advantages
Stendal was chosen as the enterprise base. Not only because it creates a sense of home for Sven Kägebein. Both founders, who met during the development stage of the software and can both look back on academic careers in the areas of mechatronics, plant engineering and information technology, agree on the advantages of the location in northern Saxony-Anhalt. Its accessibility via the ICE and motorway links impresses them in particular, together with its convenient location between Wolfsburg and Berlin which attracts commuters. “Last but not least, we also saw Stendal as a good economic sector for us. And we are not a company of many, on the contrary - we can highlight our product exceptionally”, Timur Ripke says.
Other industries should benefit from the software
The young company receives support by the investor “bmp Ventures AG” and by the funds of the venture capital fund of the state of Saxony-Anhalt. Ten employees, including six software developers, ensure that “COMAN” also reaches other industries. “Designing processes more efficiently, avoiding misunderstandings, adhering to deadlines and thus preventing unnecessary costs; this is ultimately important in any place where work is carried out in complex processes”, Mats-Milan Müller says. In this respect, the company has an eye not only on the industry of worldwide mechanical and plant engineering. Industries such as building, power plant or aircraft construction can also benefit from “COMAN” today, which successfully performed pilot projects can already confirm. Contacts for pilot projects in other construction industries have already been established, the Head of Marketing states. When it comes to the construction sector, Timur Ripke cites the negative examples of Berlin-Brandenburg airport and the Elbe Philharmonic Hall as an argument for its holistic approach. “More transparency in the processes would definitely have helped”, he thinks.
All players maintain an overview
Precisely this transparency is one of the most important advantages of the digital tool solution from Stendal. The project and scheduling software visualises the entire process chain - from the acquisition and development to the start of production. It combines the scheduling of all those involved, integrates defect tracking and progress in a central database. Deviations from the plan are displayed immediately. Project and building managers keep an overview thanks to graphic symbol codes, so-called smart objects, like robots which are linked on a visual layout or a direct CAD template. All players can thus save their own data themselves. The customer controls who should examine which areas. “Everything can immediately be saved on the building site and is stored in an audit-proof manner”, Timur Ripke explains. “This can also be done offline, regardless of where you are in the world. As soon as you are online, the status updates itself.” Here developers make sure that you can work “without much fuss”. Timur Ripke says: “Everything must be done fairly quickly on building sites. You go onto the app, click on a couple of things and everything is up to date, the current project status is now accessible at any time.”
Altmark IT company on a growth trend
“Worldwide”, “real time” and “audit-proof” are important terms in the Altmark start-up. Together with the saying “to see beyond one’s own nose”. The company is on a growth trend, and is currently devoted to the presentation of practical examples, new features, such as a dashboard for managers, and also the initiation of pilot projects. Mats-Milan Müller says: “Our digital solution should be perceived as an international tool even more - and we as drivers of innovation.” They also want to hire new employees, the Head of Marketing says, to “be able to process new customer requests, gain a foothold in new industries and capture new markets like China”.
Author: Manuela Bock